精密機器の金属部品について、
デザイン性を損なわず耐久性を改善
不可能と思われていた1工程での一体成型に成功
PROPOSER
日本を支えるものづくり企業様がお客様です。
精密な成型部品や金属部品などをご提供しています。
開発段階からお声がけいただくことも多く、
設計提案から量産化まで幅広く対応しています。
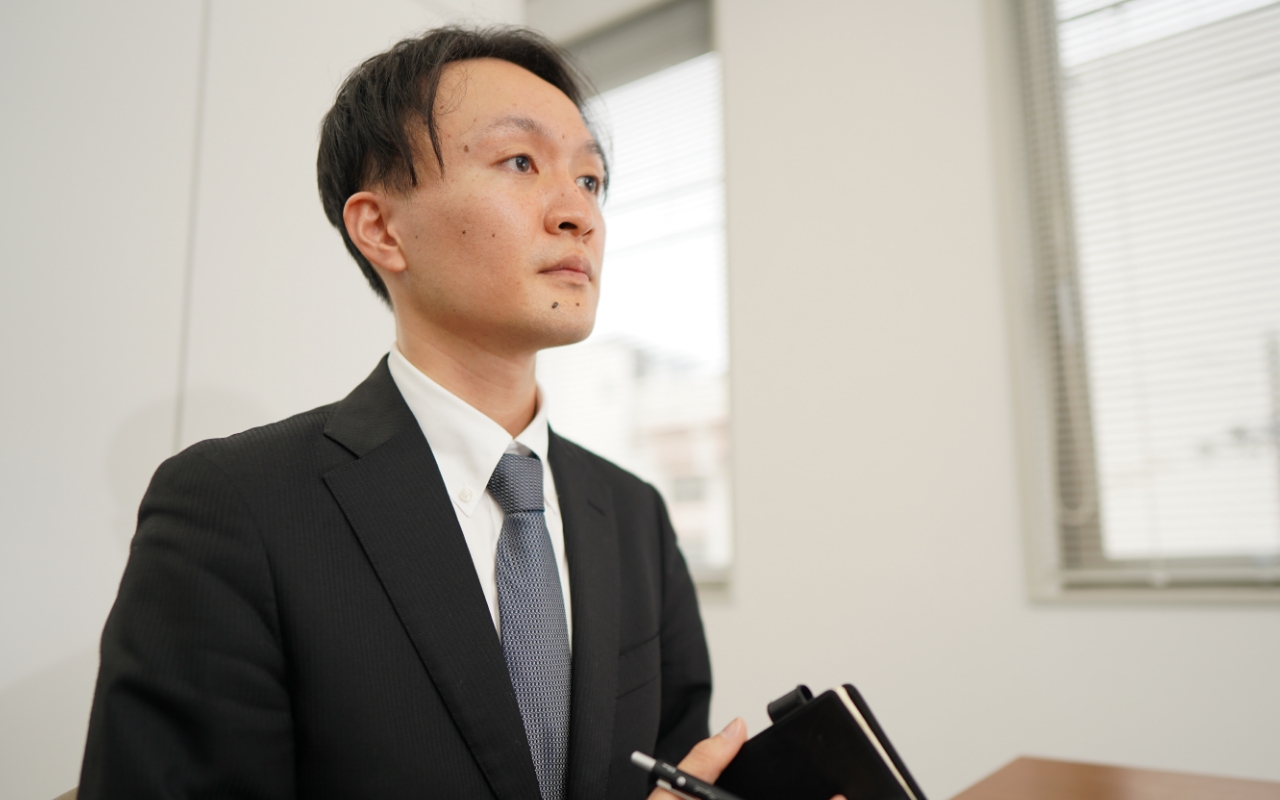
BEGINNING
精密機器のある金属部品について、強度が足りず耐久性を課題とされていました。
お客様のお困りごとをヒアリングに伺ったときにご相談いただき、プロジェクトがスタートいたしました。
デザイン性を損なわないためやむなく特殊な形状に
お客様が生産されている精密機器は、市場での競合が厳しいため、差別化戦略としてデザイン性をとても大切にされていました。 そのため、ある金属部品は力がかかる部品でありながら特殊な形状にしなければならず、コスト高になることを承知で
2種類のプレス部品を溶接接合する工法がとられていました。
この部品は溶接接合のためどうしても溶接部の強度が不足してしまい、機器の全体的な耐久性にも影響していました。
また、プレス加工2工程と溶接加工1工程の合計3工程を必要とするため、通常のプレス部品と比べてコスト高でもあります。
強度不足とコスト高の両面でこの部品はこの製品にとって大きな課題となっていました。
NETWORK
1回のプレスで形状を
どうやって加工するか
お客様は金属の材質やさまざまなプレス加工を十分に検討されたうえで、やむなく現在の2部品接合の工法を選択されています。
それを1回のプレスでどうやって加工するかが課題。
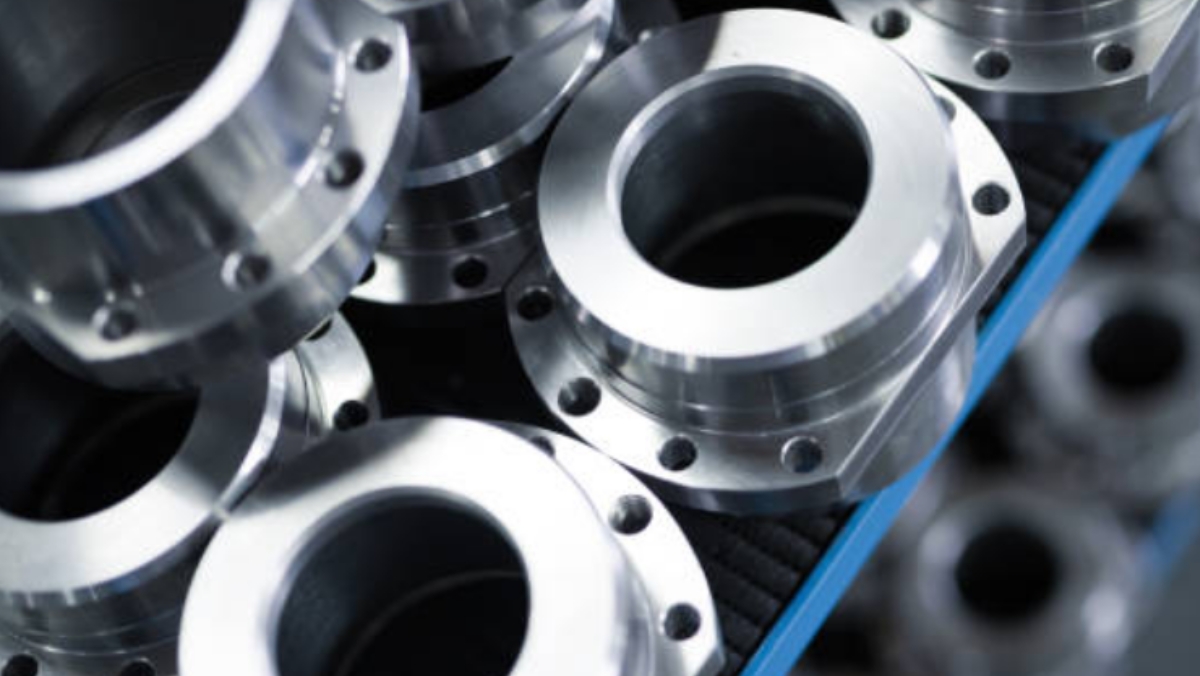
上司や技術部門と検討を繰り返し、弊社パートナー企業のプレスメーカーに相談しながら1回のプレスでどうやって加工するか検討を重ね、方策を決定。
ここであきらめたら弊社を信頼してご相談いただいたお客様に申し訳が立たない。
SOLUTION
できないとあきらめるのではなく、どうすればできるかを考える
初めは自信がないと言われていたプレスメーカーさんでしたが、何度も試作を繰り返すうちに金型の設計に手ごたえを感じるようになり、最終的には6カ月以上の期間を経て、ようやくお客様から了承いただけるレベルの試作が完成いたしました。お客様のご協力もあり何度も試作を重ねることができたからこそ、不可能と思われていた1工程での一体成型に成功できたと思います。
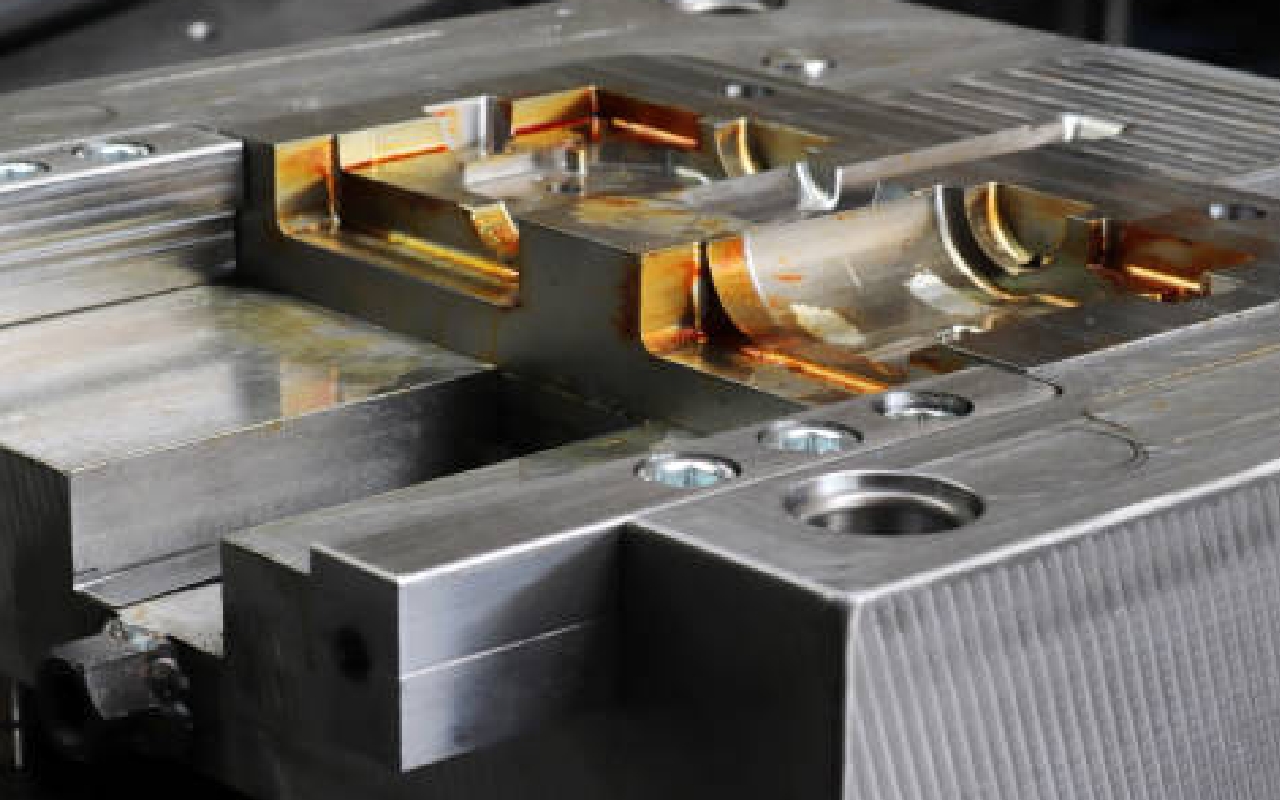
このプレスによる課題解決はお客様から非常にご評価いただき、優秀な改善提案例として賞をいただくことができました。
あきらめずに一緒に最後まで開発をやり通していただいたプレスメーカー様に感謝しています。
これからもこの精神を忘れることなく、どんなに難しい課題であっても解決できるまで続けていきたいと思います。
SOLUTION STORY
課題解決事例を見る